Sustainable Marine’s Tidal Turbine Drivetrain Completes Rigorous Tests at World-renowned RWTH Aachen University
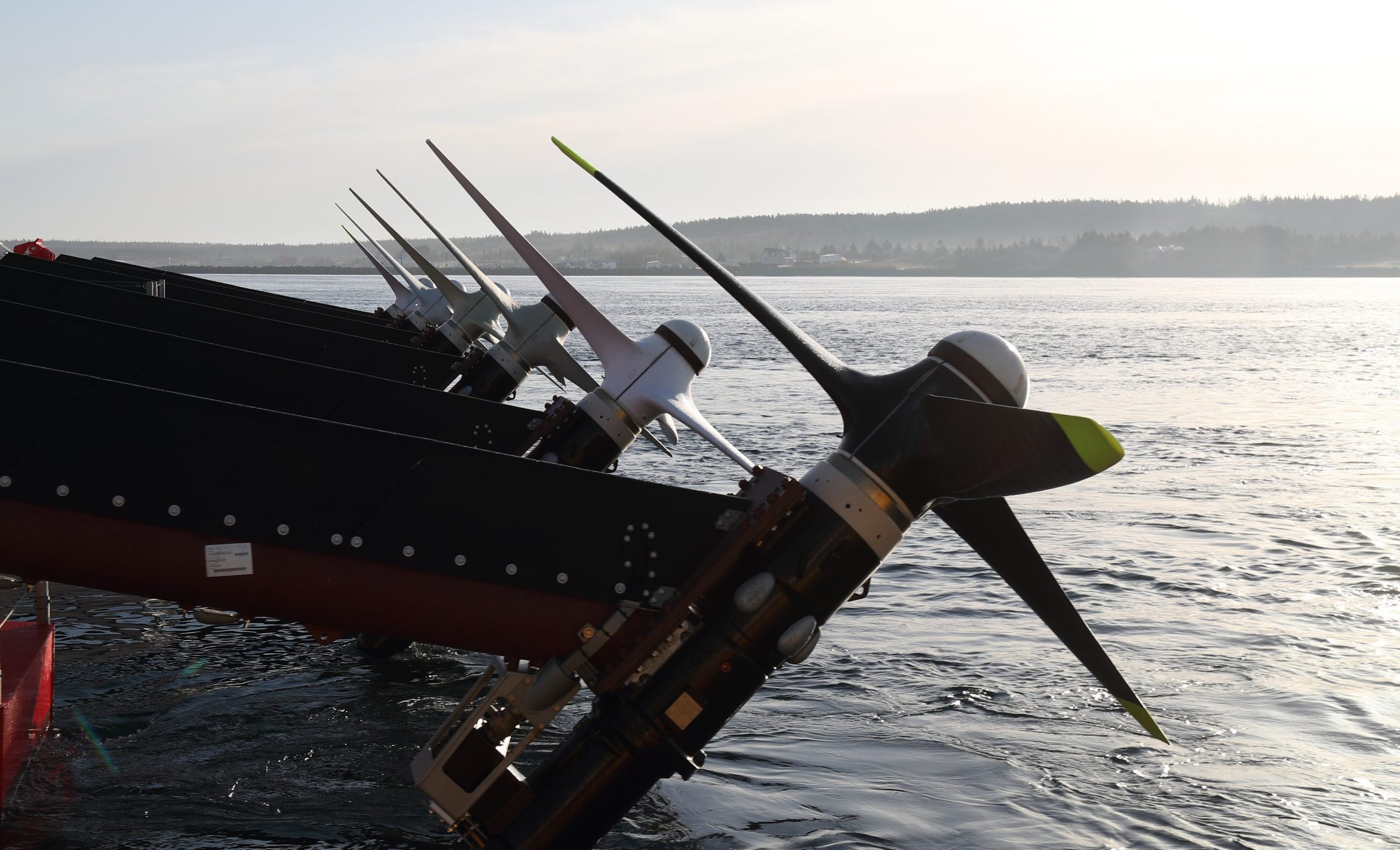
17.08.2021
SCHOTTEL Hydro, Sustainable Marine’s German engineering partner, has collaborated with the world-renowned Center of Wind Power Drives at RWTH Aachen University to test its latest generation SIT250 drivetrain.
The key component, manufactured by propulsion expert SCHOTTEL, forms the ‘powerhouse’ of Sustainable Marine’s pioneering floating tidal turbine, converting torque – or rotation of the blades – into electricity.
The ‘accelerated lifetime testing’ was successfully completed in a 6-month period, replicating five years of operation in the Minas Passage, Bay of Fundy, Nova Scotia, Canada – home to the highest tides on earth.
The site will play host to Sustainable Marine’s Pempa’q Project involving the world’s first floating tidal energy array, delivering up to 9MW of energy to Nova Scotia’s grid, powering around 3,000 homes per year.
A unique, tailor-made test rig was built within the University’s Center for Wind Power Drives (CWD), to test the drivetrain. It formed part of the “OsT” project, led by SCHOTTEL Hydro and funded by the German Federal Ministry for Economic Affairs and Energy (FKZ 03EE4001A).
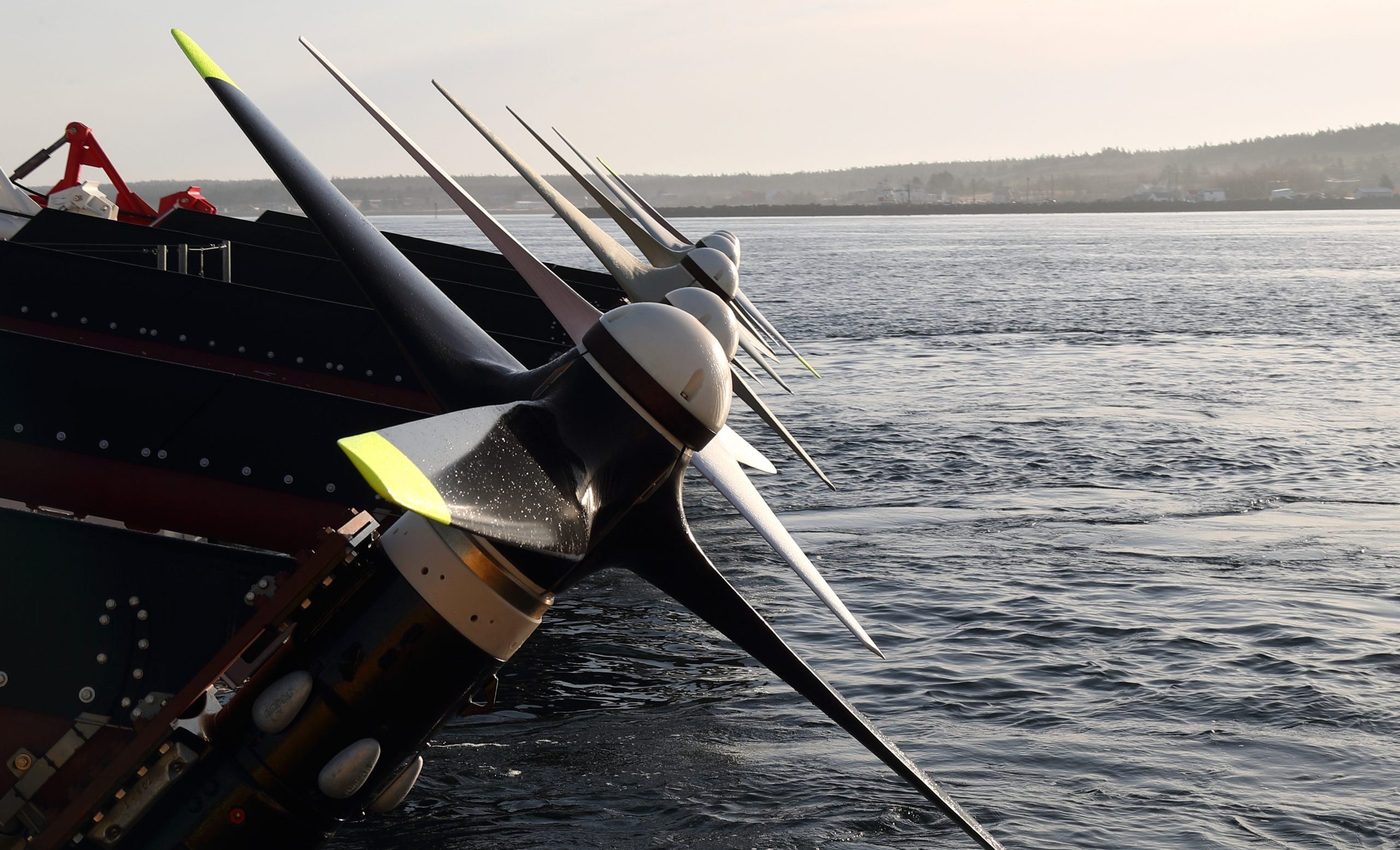
“Our latest testing project with Aachen University marks another significant step forward for our tidal energy technology and the broader Pempa’q Project,” said Ralf Starzmann, Vice President of Business Development at Sustainable Marine. “The durability and survivability of our platforms is paramount alongside their energy generating capacity at competitive costs. It was particularly important to prove the drivetrain could withstand five years of operation at the Minas Passage site, with this being the planned maintenance interval period. Rigorous independent assessments with world-class institutes like Aachen University play a key role providing credibility and confidence in the technology.”
Sustainable Marine’s SIT250 drivetrain has a grid-ready electrical power rating of 70kW. The system consists of a rotor hub, slow speed shaft, planetary gearbox and asynchronous generator.
As part of the novel test procedure a total of four independent hydraulic cylinders were used to apply simultaneous testing involving multiple load components. Further a 125 kW motor was used to substitute the torque generated by the rotor.
Following 2467 hours on the test rig, 152MWh of electrical energy was fed back by the drivetrain, equating to around one year’s electricity supply for 50 German homes. Post testing the drivetrain was decommissioned and subjected to a thorough inspection.
“The test program was divided into two main sequences,” said Dennis Bosse, Managing Director at the Center for Wind Power Drives. “The first period focused on the rotating components, including the bearings and gearbox, where fatigue damage is caused by constant loads, involving torque, thrust as well as transverse force and bending moments were applied. During this period the drivetrain ran for 1800 hours at rated power. The second period focused on the static components including the drivetrain housing where fatigue damage is caused by variation of the loads. Components oscillated simultaneously with multiple combinations and load amplitudes. Ultimately, the testing proved that the SIT250 drivetrain is capable of withstanding the significant challenges posed by the FORCE Test Site in the Bay of Fundy.”
RWTH Aachen University is located in North Rhine-Westphalia, and is the largest technical university in Germany, with more than 45,000 students enrolled in 144 study programs. The CWD is globally renowned for testing wind power drives.